Rmc plant silo is the important storage system for powder materials of concrete batching plant. In the concrete producing process, powder materials (like cement, fly ash and so on) are the main batching ingredients, and their properties and ratios directly determine the quality of the final concrete product. LUTON engineers have designed various high-quality powder storage systems based on the production capacity, environmental characteristics, transportation distance, and methods of different ready mix concrete plants.
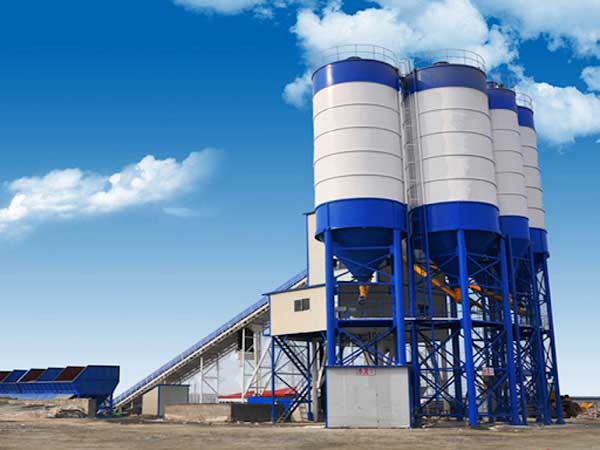
Dust Removal
Pressure Safety Alarm
Discharging Control
Convenient Maintain
Material Level Detection
Automatic Weighing
Broken Arching Device
Durable Structure
Bolted Type Rmc Plant Silo | 50T | 80T | 100T | 200T | 300T | 500T |
Barrel Diameter (m) | 3 | 3 | 3 | 4.5 | 4.5 | 5.4 |
Barrel Height (m) | 6 | 9 | 11 | 13 | 17 | 19 |
Main Functional Parts Of Rmc Plant Silo
As we all know, the powder silo of a ready mix concrete plant is a device for storing various powders. In order to store powder with high quality and stability, in addition to insulated and moisture-proof silos, the powder silo is also equipped with:
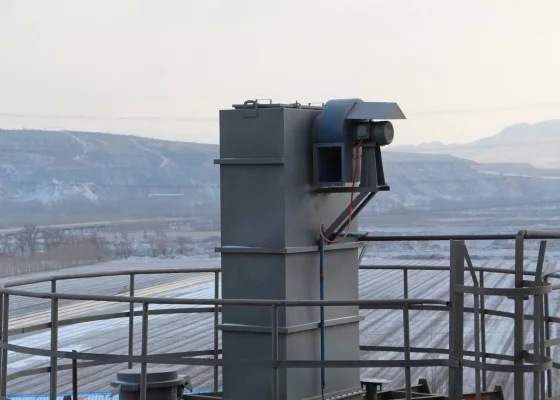
Dust Removal System
Collect the dust scattered in the air, environment friendly and reduces powder loss. Common dust removal devices are:
- Bag Filter: Filter and separate the dust by filter bag. Suitable for treating the dust with small particle size.
- Cyclone Dust Collector: Separate the dust by centrifugal force. Suitable for treating the dust with large particle size.
- Wet Dust Collector: Collect and separate the dust by water. Suitable for handling high-humidity dusty air.
- Electric Dust Collector: Collect and separate dust by an electric field. Suitable for handling moist and thick dusty air.
All these dust removal equipment has their own characteristics, suitable for different dust removal of different types of concrete batching plant.
Material Level Detection System
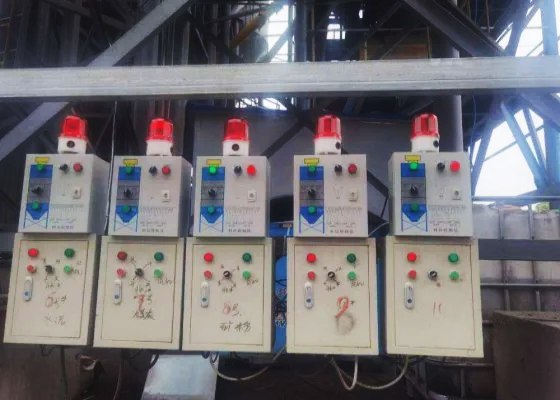
By detecting volume of the powder in the silo, it alarms the situations that material is above or below the preset level. In this way, we can get the full- or short- storage situations.
Pressure Safety Alarm System
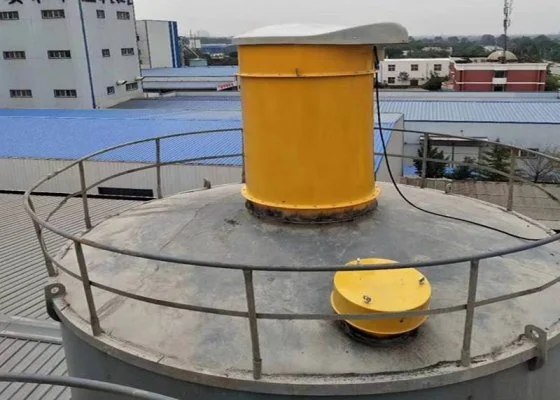
Detect the air pressure in the bin. When the air pressure is above the normal value, trigger the alarm system, and open the pressure safety valve to release the pressure in the bin to prevent the explosion accident.
Maintenance Platform and Staircase
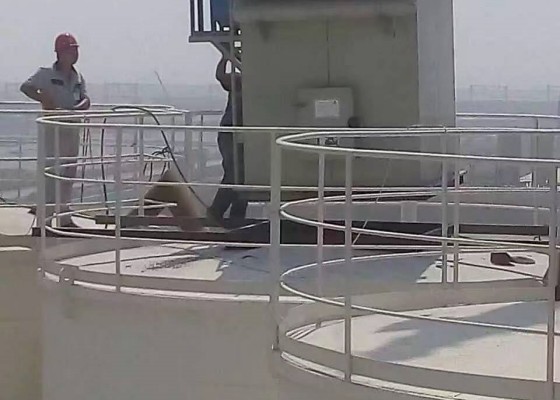
A safe passage for staffs to inspect and maintain the powder silo.
Weigh System

Measure the weight of the powder materials for accurate concrete proportion.
Discharging Control Butterfly Valve
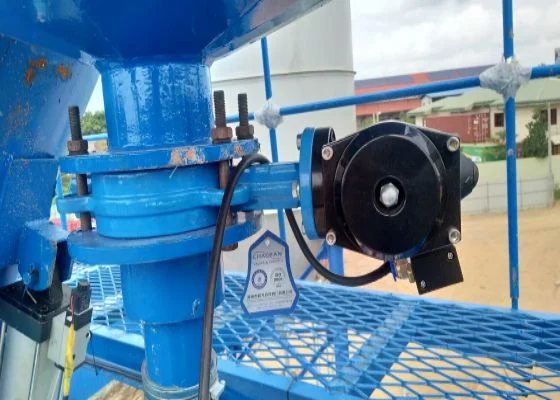
Based on the weighing system data, open and close the valve to control the conveying of powder materials.
Arch Broken Device
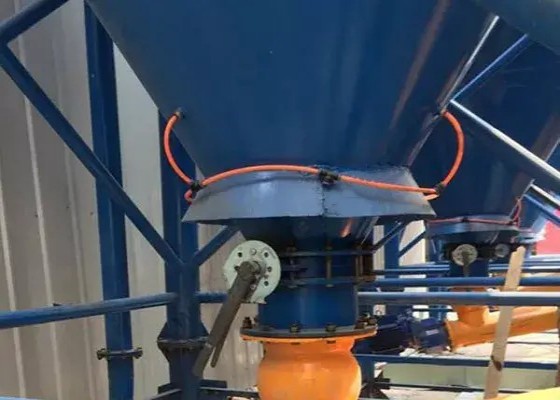
The arch broken device is installed on the cone bottom of the silo. The small electromagnetic reversing valve located in the gas control box is used to control the release of compressed air, aiming to avoid powder blockage caused by long accumulation.
Types Of Rmc Plant Silo
For different transportation, disassembly and storage needs, our engineers have designed different types of rmc plant silos.
According to different assembly methods:
Welding Type Rmc Plant Silo
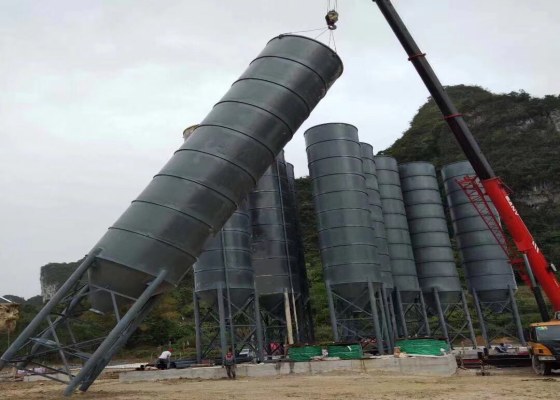
Welded type powder silo is also known as integral powder bin. Because of its inseparable, it can only be transported as a whole. So, it is suitable for short distance transportation.
In addition, only the overall welded powder silo under 50 tons can be packed for shipping. But this integral structure has the advantage of saving time and labor for installation.
Bolt Type Rmc Plant Silo
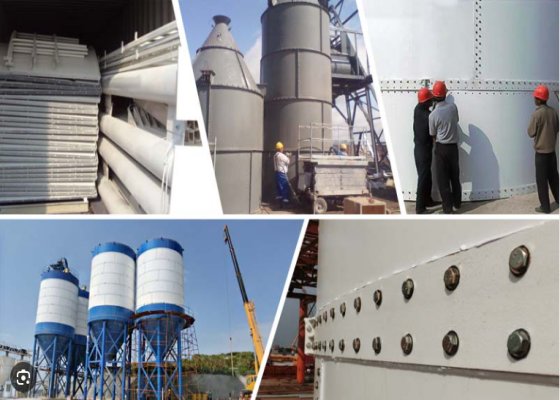
Bolt type powder bin, also known as the sheet powder bin, is shipped in pieces after production and fixed into a whole silo with screw bolts after arriving at the destination.
The fragmentation design is suitable for long distance transportation. So, it is the best choice of exportation.
However, the split structure also means long installing time. What’s more, the bolt fixing method needs to pay special attention to the sealing of the powder silo.
Telescopic Type Rmc Plant Silo
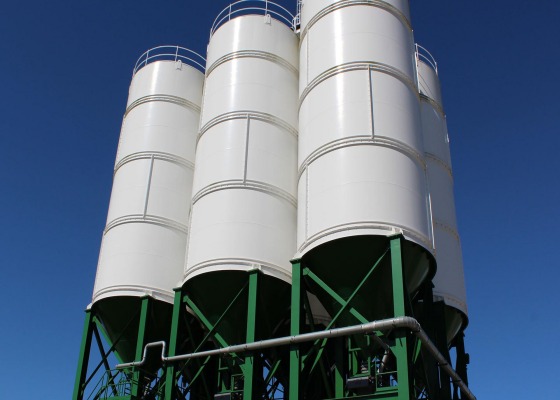
Telescopic powder silo can be divided into two or three parts. This type can adapt to both long-distance packing transportation and fast site installation. The type of powder silo is limited to the 50 tons model.
According to the structure:
Vertical Type Rmc Plant Silo
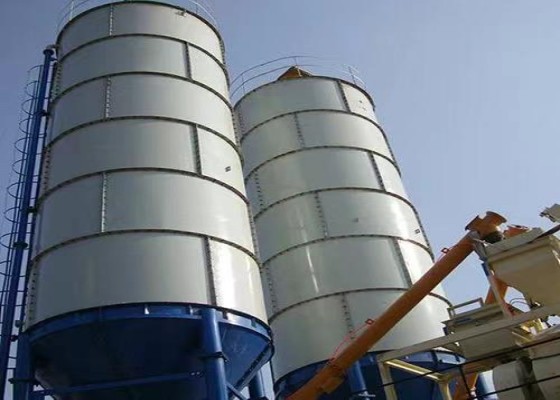
The vertical powder silo has a tall cylindrical barrel and solid support legs, deeply buried in the foundation. The bottom of the silo is conical for quick discharge.
Vertical powder bin, because of its height characteristics, is necessary to make a solid foundation according to the actual situation of the weight and height of the bin before installation.
Horizontal Type Rmc Plant Silo
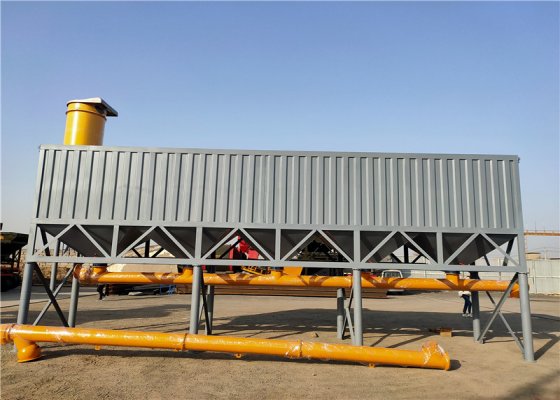
The horizontal rmc plant silo is a cuboid storage container supported by several steel legs. The bottom of the silo is a square discharging cone. The silo body is made of corrugated steel plate to effectively prevent the deformation.
Horizontal powder bin is especially suitable for packing and more popular in countries with strict height limits.
How Does Rmc Plant Silo Work
Step1
Cement and other powder are transported to the construction site through the bulk cement truck. When the conveying pipeline is connected with the feed pipe of the powder tank, the cement and other powder in the tank truck are continuously transported to the inside of the powder tank, until the level gauge detects that the powder in the silo reaches the full position. Then the feeding is over.
Step2
In the process of conveying powder, the dust removal device begins to work. For the commonly used bag filter, the vibrator of the filter will shake off the dust particles attached to the filter bag, to prevent blocking the bag and burst the warehouse.
Step3
In this process, once the bag is blocked, the pressure on the top of the silo will be higher than the common value, and the pressure detector will alarm, then automatically open the pressure safety valve to release the air pressure in the bin and prevent the explosion accident.
Step4
In the plant working process, the central control system will release discharging instruction to the air compressor to open the pneumatic discharge butterfly valve located at the bottom of the powder silo cone. Then cement or fly ash powder will naturally fall down, through the connected spiral conveyor, directly to the concrete mixing plant powder weighing bucket. At the same time, when the measured weight reaches the preset value, the screw conveyor is shut down by the control system, and the powder conveying is done and ready for the next task.
Step5
When it comes to silo unloading, the phenomenon of “arch” may occur at the bottom of the bin, or the pressure at the bottom of the bin is too high, the control system will issue instructions to release the compressed air of the arch breaking device, break the blockage caused by powder accumulation, and ensure the smooth supply of cement powder or fly ash.
Step6
When a fault occurs in the process of powder conveying, close the manual discharge butterfly valve at the bottom of the bin immediately to prevent powder overflow and material waste.
Operation Of Rmc Plant Silo
Note For The Safe Operation Of Cement Powder Bin
To ensure the durability of the cement bin, the daily inspection and normal operation of the arch breaker are very necessary:
- Regularly check whether the pipe and connection of the arch breaker have the phenomenon of loose or air leakage, and whether the pneumatic components are flexible.
- Regularly check whether the structure of the arch broken device in the cement bin is damaged, whether the welding place of the hanging and support device is firm, and whether the bolts are loose.
- The piston of the broken arch device should be removed frequently to ensure that the device is clean.
Inspection Of The Dust Removal Equipment
According to the actual situation, open the butterfly valve to clean out the collection every 4-5 hours to collect dust. A pneumatic butterfly valve automatically controlled by the concrete plant software operating system can also be installed and opened regularly for the normal discharge of dust. At the same time, be sure to regularly check and sort out the filter element of the dust collector on the silo top.
Avoid Moisture And Arch Of The Material
Cement powder in storage, if the sealing is not strict, is easy to lead to dry powder moisture and arching. Once the arching occurs, open the arch breaking device immediately.
Each part of the cement powder bin in the usage needs careful and regular maintenance and inspection, as well as should find and solve problems in time, so as not to cause unnecessary trouble.
Hot Models Of LUTON Concrete Batching Plant
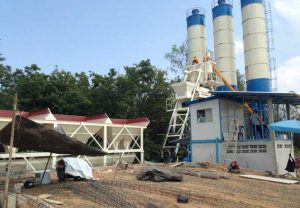
HZS50 Skip Bucket Concrete Plant Installed In Thailand
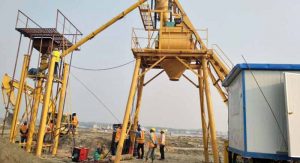
HZS35 Concrete Plant installed in Bangladesh
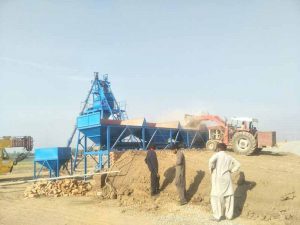
HZS25 Concrete Plant Installed In Pakistan
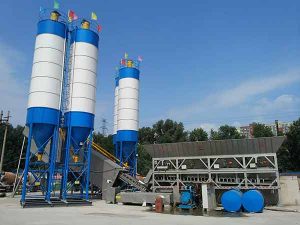
HZS90 Concrete Plant in UZ
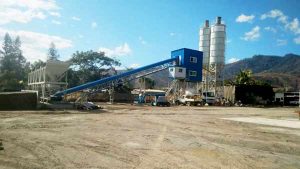
HZS60 Belt Type Concrete Plant in East Timor
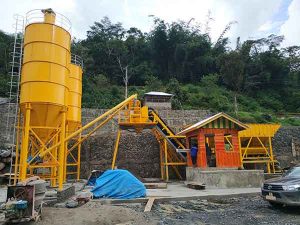