Concrete batch plant control system is the crucial part for automatic production. The performance of control system directly affects the whole concrete process and the quality of the concrete products. Know more about it and make your plant more profitable.
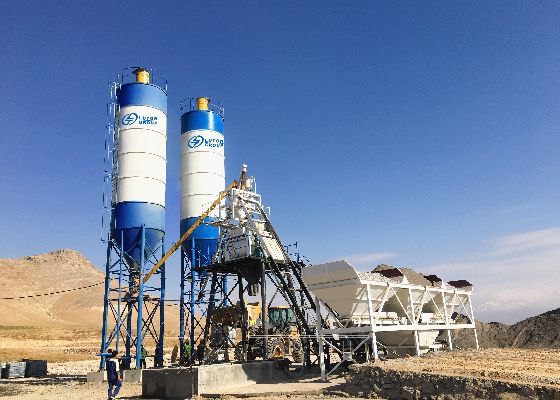
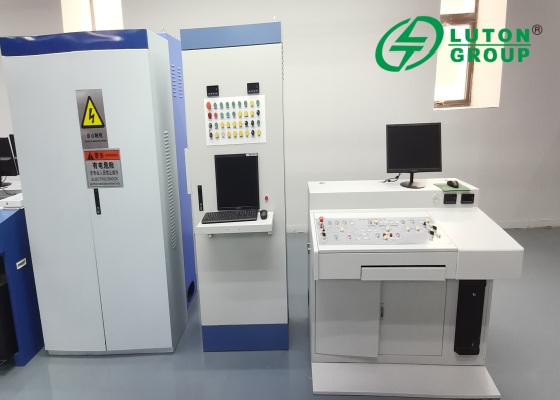
The Roles Of Concrete Batch Plant Control System
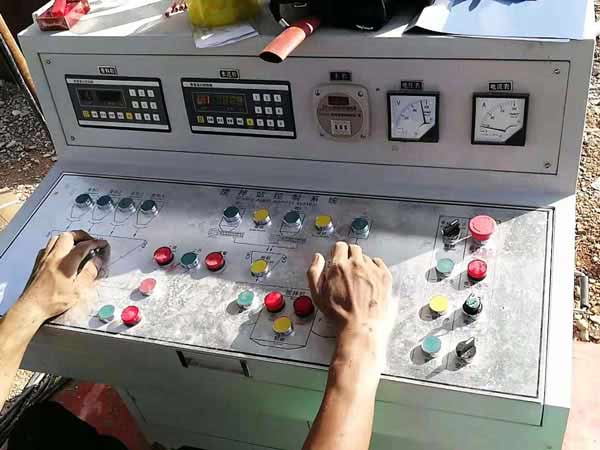
The electrical control system of the concrete mix plant is mainly used to control and monitor the production process of the mixing plant, ensuring the stability and quality of concrete production. Its functions include but are not limited to the following:
- Automatically control the production process of the mixing plant to improve production efficiency and quality.
- Monitor and adjust parameters such as raw material placement, mixing time, and mixing speed to ensure consistency in concrete manufacturing.
- Real time monitoring of equipment status, alarms, and fault diagnosis to improve equipment reliability and safety.
- Data collection, analysis, and reporting provide decision-making basis for production management.
Working Principle Of Concrete Batch Plant Control System
Concrete batch plant control system is based on PLC (Programmable Logic Controller) or DCS (Distributed Control System) to achieve automatic control. Its working principle is as follows:
- Collect on-site data through sensors and instruments, including parameters such as raw material placement, mixing drum speed, temperature, pressure, etc.
- Transfer the collected data to the PLC or DCS system for processing and analysis.
- According to pre-set control algorithms and logic, control the actuator, such as opening and closing valves, starting motors, etc., to achieve automatic control of the concrete production process.
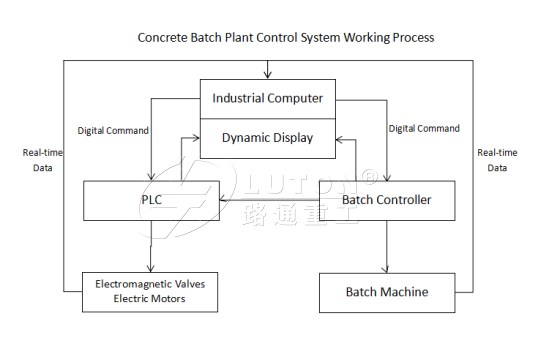
System Composition And Main Components
Concrete plant control system consists of the following components:
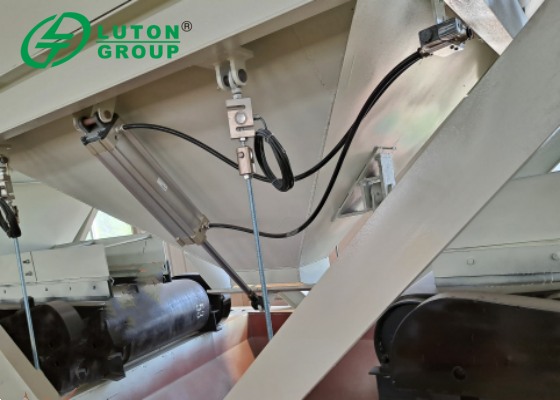
- Sensors and instruments: used to collect on-site data, such as flow rate, temperature, pressure, etc.
- Signal conditioner: converts the signals collected by sensors into standard signals and inputs them into PLC or DCS systems.
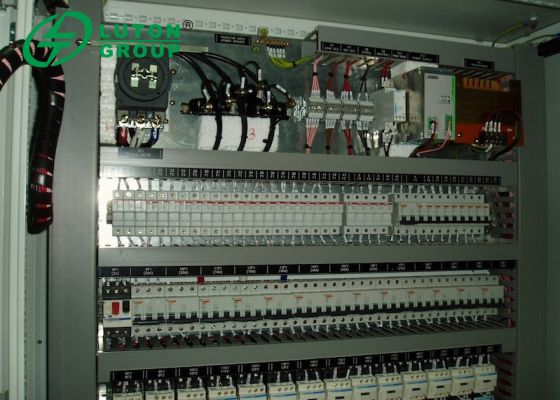
- PLC or DCS system: responsible for data processing, control algorithm execution, and equipment status monitoring.
- Execution mechanism: including servo motors, hydraulic systems, etc., used to control the start stop and adjustment of equipment.
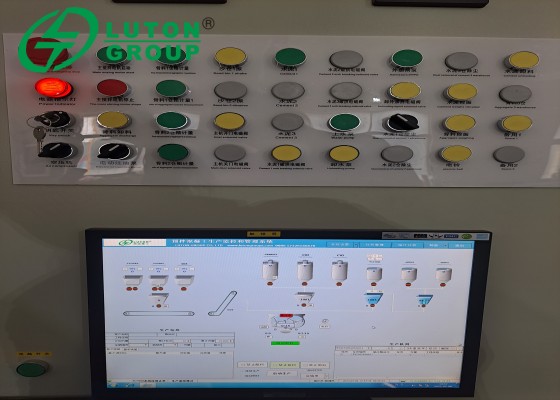
- Human machine interface: Provides an operation interface for operators to monitor equipment status, adjust parameters, etc.
Common Faults And Maintenance Solutions
In the concrete batch plant control system, common faults include damage to electrical components, sensor failures, communication interruptions, etc. For these faults, the maintenance plan is as follows:
- Regularly inspect and maintain electrical components, such as replacing aging relays, fuses, etc., to ensure the normal operation of electrical components.
- Regularly calibrate and test sensors, and replace damaged sensors in a timely manner.
- Check communication lines and interfaces to ensure smooth data transmission.
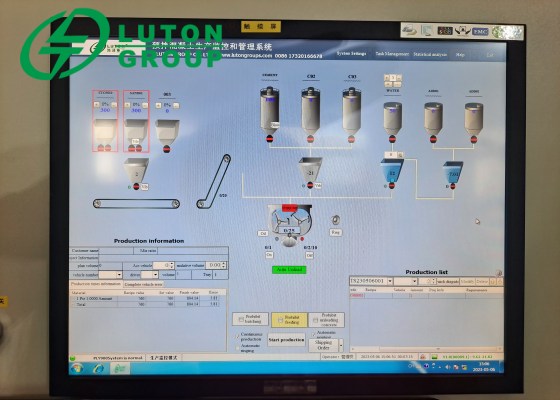
Development Prospects And Cutting-edge Related
With the rapid development of industrial automation and informatization, the electrical control system of concrete mixing plants is also constantly evolving and innovating. The future development prospects include the following aspects:
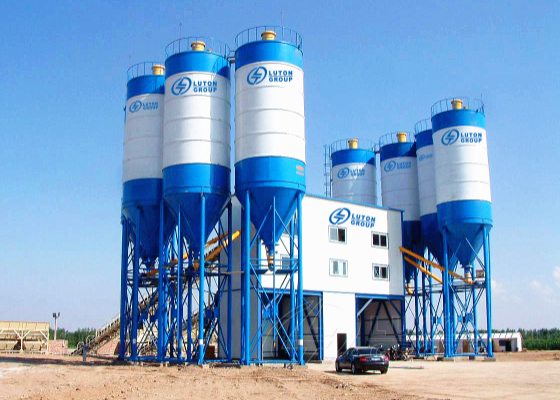
- Intelligence: Applying artificial intelligence technology, the electrical control system will be with more intelligent equipment operation, data analysis, and fault prediction. By learning algorithms and big data analysis, the system can adjust process parameters based on real-time data, improving production efficiency and quality.
- Cloud platform integration: Through cloud platforms, managers can monitor device status, develop production plans, and diagnose faults anytime and anywhere, improving the efficiency and accuracy of production management.
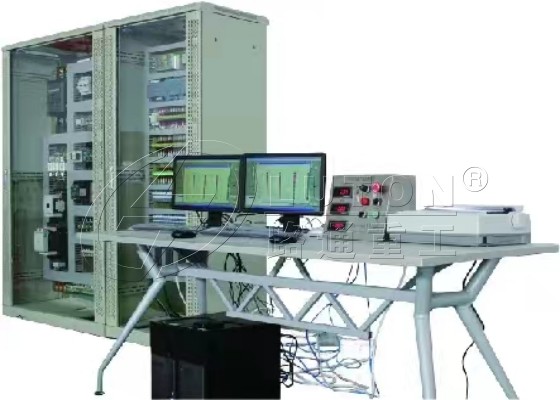
- Automation optimization: With the help of advanced algorithms and control technology, for example, by optimizing the mixing process and controlling parameters, the efficiency, quality, energy conservation, and emission reduction of concrete production can be maximized.
- Environmentally friendly: In the development of electrical control systems, more and more attention is being paid to environmental protection and sustainable development.
- Data sharing and collaboration: The development of electrical control systems for concrete mixing plants also involves data sharing and collaboration. By interacting and sharing data with other engineering equipment and management systems, comprehensive production collaboration and optimization can be achieved.
In the cross cooperation with other industries, cutting-edge technologies in the electrical control system have also been applied. For example, combining IoT technology, big data analysis, and machine learning can achieve more efficient and flexible concrete production methods. All these provide more accurate production data and management decision-making basis.
Summary
The concrete batch plant control system plays an important role in concrete production, not only improving production efficiency and quality, but also helping to achieve automation, intelligence, and sustainable environmental development. With the continuous progress of technology, the electrical control system of concrete mixing plants in the future will continue to innovate and be applied in a wider range of fields, making contributions to the development of infrastructure construction.